
What is an Electrical Drives
Electrical Drives :Definition, Block diagram, Classification , advantages and disadvantages.
Whenever the terms "motor" or "generator" are used, we tend to think that the speed of rotation of these machines is completely controlled by the frequency of the applied voltage and source current. However, the rotation speed of the motor can also be accurately controlled by implementing the concept of driving.
Test your Basics:Electrical Drives
The main advantage of this concept is that motion control can be easily optimized with the aid of a drive. Simply put, the system that controls the movement of a motor is called an electric drive.
A typical drive system consists of an electric motor and a complex control system that controls the rotation of the motor shaft. Today, this control can be easily done with the help of software. As a result, control becomes more and more precise, and this drive concept also provides ease of use.
Evolution of Drive :
• Came into picture with the invention of wheel in the proto historic period of 3500 BC.
• Till 18th – 19th century : Not much conscious effort in the control of motion
• Conscious effort to control motion : advent of steam governors
• Advent of electric motors in 19th century led to the development of electric drive
• Conscious automatic control of drive became more wide spread.
This drive system is widely used in many
industrial and home applications such as factories, transportation systems,
textile mills, fans, pumps, motors, robots, and so on. The drive is used as a
diesel or gasoline engine, gas or steam turbine, hydraulic prime mover motor
and electric motor.
Now entering the history of electric drives,
it was first designed by B.S. Iakobi in Russia in 1838, when he tested the DC
motor provided by the battery and propelled the boat. Even industrial
adaptation occurred many years after about 1870. Today, the application of
electric drives can be seen almost everywhere.
Definition of Electric Drive:
Systems employed for imparting motion and its control. An electrical drives employing electric actuator or motor as the prime mover. A system used to control the movement of a motor is called as an electrical drives.
In other words, a
driver using an electric motor is called an electric driver. Electric drives
use any prime mover, such as hydraulic motors or electric motors as the main
energy source. The prime mover provides mechanical energy to the drive for
motion control.
Applications of electrical drives:
It is widely used in industrial and domestic applications such as
• Transportation systems
• Paper mills
• Cement Mills
• Textile mills
• Sugar Mills
• Steel Mills
• Electric Traction
• Petrochemical Industries
• Electrical Vehicles
Block diagram of the electric drive:
The figure below
shows the block diagram of the electric drive. The load in the figure
represents various types of equipment, including fans, pumps, washing machines
and other motors. Determine the electrical load requirements based on speed
and torque. Choose a motor suitable for the load capacity as the load driver.
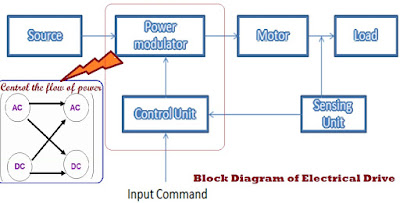
Block Diagram
Various components of electrical drives:
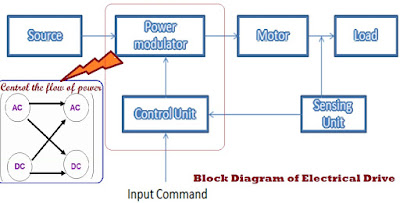
The main components of the electric drive are the power modulator, motor, control unit and sensing unit. Their components will be described in detail below.
Source: For electrical drives sources are AC and DC. AC sources are single phase or three phase AC supplies
Power modulator: Power modulator performs the following functions
• Modulates power flow from the source to the motor.
• During transient operations, such as starting, braking and speed reversal, it restricts source and motor current within permissible values. Excessive current drawn from source may overload it.
• It converts electrical energy of the source in the form suitable to the motor. For example, if the source is direct current and an induction motor is used, the power modulator converts the direct current into alternating current
• It also selects the operating mode of the motor, i;e motoring or braking.
The power modulator can adjust the output power of the power supply. It controls the power from the power source to the motor so that the motor transfers the speed-torque characteristics required by the load.
During transient operations such as starting, braking and speed, excessive current drawn from the power supply can be reversed. Excessive current drawn from the power supply may overload it or cause a voltage drop. Therefore, the power modulator limits the source current and the motor current.
Control unit:
The control unit controls the power modulator, which operates at a lower voltage and power level. The control unit also operates the power modulator as required. It also generates commands to protect the power modulator and motor. Input the command signal, from the input to the control unit, adjust the working point of the driver.
Sensor:
It senses certain
drive parameters, such as motor current and speed. It is mainly used for
protection or closed-loop operation. From Motor it senses Speed ,Torque, Position, Current and Voltage from lines or from electric
motor terminals. From Load it senses Torque
and Temperature.
Advantages of electric drives:
The following are the advantages of
electric drives.
· Electric drives have very large torque, speed and power ranges.
· Their work is not affected by environmental conditions.
· The electric drive has no pollution.
· The electric drive runs on all quadrants of the speed torque plane.
· The drive can be started easily without refueling.
· The efficiency of the drive is high because of low losses.
Disadvantages of electric drive:
· The power failure completely disabled the entire system.
· The application of the driver is restricted because it cannot be used in places where there is no power supply.
· Will cause noise pollution.
· The installation cost of the system is high.
· Its dynamic response is poor.
· The output power obtained from the driver is low.
· During conductor failure or short circuit, the system may be damaged, so some problems will occur.
Selection Criteria of Electrical Drives:
The choice of electric drive depends on many factors. Some important factors are.
1. Requirements for steady-state operating conditions: Properties of speed torque characteristics, speed regulation, speed range, efficiency, duty cycle, working quadrant, speed fluctuation (if any), rating, etc.
2. Transient operation requirements: Values for acceleration and deceleration, starting, braking and reversible performance.
3. Requirements related to source: Power supply type and its capacity, voltage size, voltage fluctuation, power factor, harmonics and their impact on other loads, the ability to accept regenerative power
4. Capital and operating costs, maintenance requires life.
5. Space and weight restrictions (if any).
6. Environment and location.
7. Reliability.
Types of Electrical Drives:
A variable speed drive for controlling a DC motor is called a DC drive, and a variable speed drive for controlling an AC motor is called an AC drive.
AC drives are used to drive AC motors, especially three-phase induction motors, because in most industries they have an advantage over other motors. In industrial terms, AC drives are also called variable frequency drives (VFD), variable speed drives (VSD).Based on the application and demands, drives are classified into various categories shown in below figure: